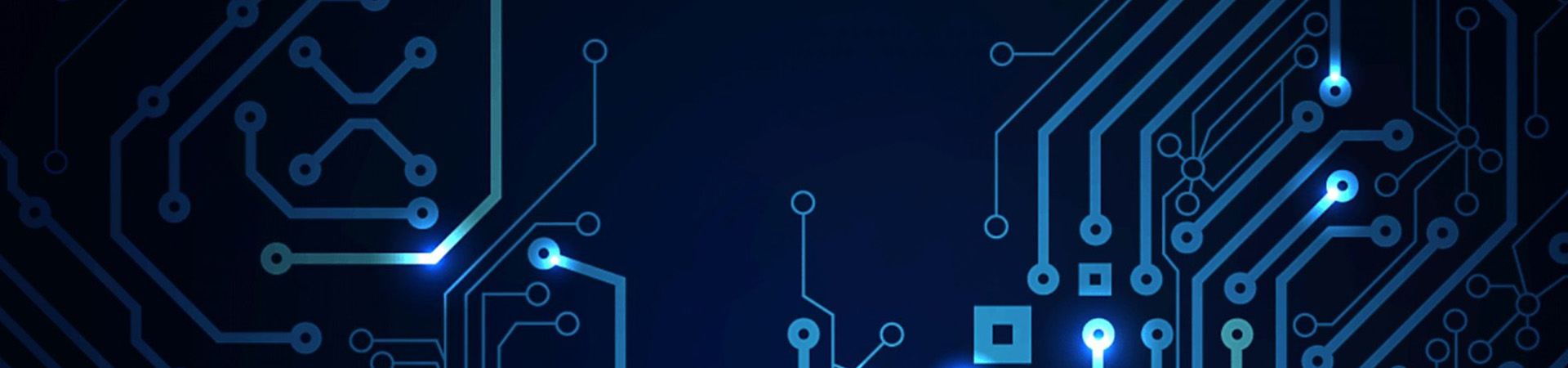
Flexible PCB Manufacturing Process - How Flex PCBs Are Manufactured?
As the world is evolving, printed circuit boards, or PCBs are becoming core components of various electrical devices. With so many technologies coming up every day, electrical devices are becoming more efficient and smaller. This is the reason why rigid PCBs are no longer compatible with today’s electrical devices. Instead, device manufacturers are now integrating flexible PCBs or flex PCBs, which offer flexibility similar to rigid PCBs.
This blog will dive into the manufacturing of PCBs, the techniques that are used to design flex PCBs, and more.
Steps Undertaken to Manufacture Flexible PCBs
The process of PCB manufacturing is quite intricate. In most cases, the process is similar to the rigid PCBs. Flexible PCB manufacturing follows sheet-by-sheet processing, which is the same process followed for rigid PCB boards. The following are the steps to manufacture flexible PCBs:
1. Cutting the Lamination of Copper Clad
The flexibility of PCBs ensures that the core materials should be processed in rolls. It is essential to plan and design the utilisation rate to meet the different product sizes. When the planning part is done, the materials are cut down into required sizes that would fit the size of the products. To obtain the copper foil sheet in the required size, it is important to cut the copper coil with the necessary tool.
2. Preparing the Material
Being a good conductor of electricity, copper foil sheets are cleaned and etched. This gives a smooth surface on which the circuit would be printed.
3. Circuit Printing & Etching
Using etching and photoresist, the design layout of the circuit is printed on the material. It is one of the crucial steps in the manufacturing of flexible PCBs. On the copper foil, a photoresist material will be integrated. Using UV light, the material will be hardened.
Photoresist materials used in the flexible PCB manufacturing process are mainly of two types. After the photoresist part is done, photomask alignment takes place. The photomask will be placed on the substrate, and UV light will be torched through the mask, where the photoresist material will be exposed in the given pattern. The photoresist part, which was not lit up by the UV light, will be removed. The purpose of this process is to obtain the substrate that has the circuit printed on it.
The material sheet will be rinsed with an etching solution to remove the unexposed copper layer that has not been protected by the photomask, leaving behind the required circuit.
4. Component Placement
After the circuit printing process, it’s time to place the component on the flexible PCB. Two technologies are used to mount the components on flexible PCBs. These technologies are through-hole technology and surface mount technology.
5. Soldering
To solder components on flexible PCBs, either the reflow soldering technique or the wave soldering technique is used. This step takes place after the component placement process is completed.
6. Testing
Testing is an essential part of the manufacturing process of flexible PCBs. Testing flex PCBs ensures that they meet the required mechanical and electrical specifications. Furthermore, to check whether the flexible PCBs have any defects, it is important to test them using different methods. Electrical testing, visual inspection, and functional testing are some of the testing methods that are used to test the efficiency of flex PCBs.
7. Cover Layer Attachment:
In a flex PCB, a cover lay is a protective layer used to insulate and shield the conductive traces while maintaining the board’s flexibility. It serves a similar function to the solder mask in rigid PCBs but is specifically designed for flexible circuits. The cover lay is pre-cut to match pad openings and component areas. Then cut coverlay is laminated onto the flex PCB using heat and pressure.
8. Surface Finish:
Plating the exposed copper with tin or gold to avoid oxidation and to provide solderability.
Once the circuit pattern is defined, the exposed copper pads then undergo a surface finish treatment to prevent oxidation. There are many surface finish methods used in the flex PCB manufacturing process. The most common surface finishes for flex PCB include Immersion Gold and Immersion Tin.
9. Stiffener Attachment
To ensure flex PCBs are in working order, stiffeners are attached to the PCBs. This element gives flexible PCBs the required protection and support. Stiffeners are often made with materials like steel and FR4. To attach stiffeners to the flex PCBs, adhesives are used.
10. Routing, Electrical Testing & Final Inspection:
To finalize the PCB, it is cut into its required shape. A probe is then used to check for any open circuits or short circuits. For Flex PCBs, key specifications such as size, FPC thickness, coverlay, surface finish, and stiffener requirements are verified. A visual inspection is also performed using a magnifying glass to ensure the PCB meets appearance standards.
Conclusion
Manufacturing high-quality flexible PCBs can strengthen the base of many electrical components. If the flexible PCB undergoes an intricate manufacturing process from design layout to testing, they can be integrated into the electrical systems well.
We at PCB Power understand the importance of flexible PCBs to support different electrical devices. Thus, we ensure a reliable flexible PCB manufacturing process.
Get an instant quote for your next flexible PCB requirements.