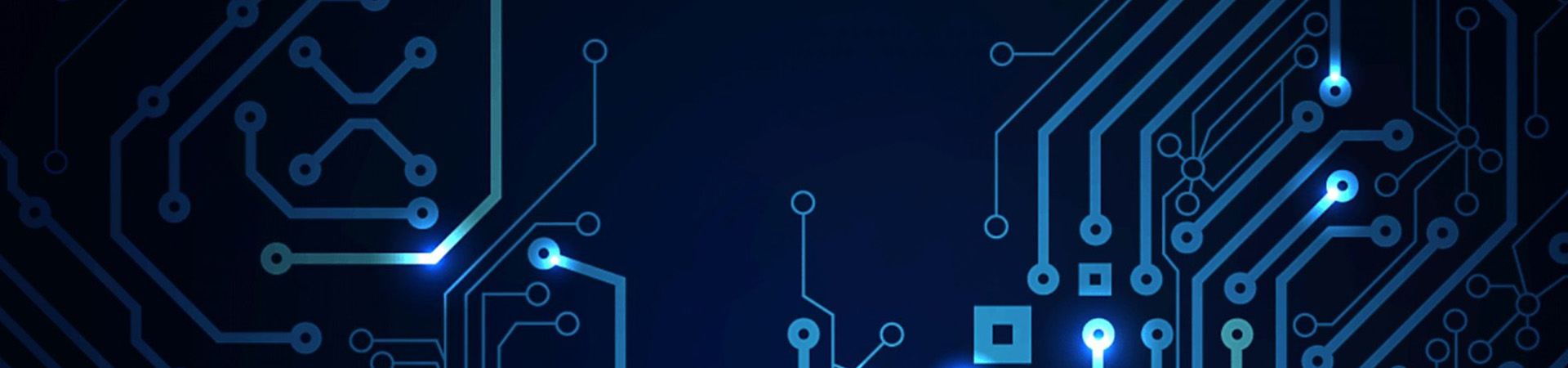
The SMT Footprint Guide Every Engineer Should Bookmark
In the realm of PCB assembly, precision is paramount. A single miscalculated dimension or misaligned pad can cascade into production delays, material waste, and costly rework. Among the most critical yet often overlooked aspects of PCB design is the accuracy of SMT (Surface Mount Technology) footprints.
Whether you're developing prototypes or scaling to high-volume production, ensuring that every surface-mount component interfaces correctly with your board design is fundamental to project success. This comprehensive guide examines the technical intricacies of SMT footprints, their impact on manufacturing outcomes, and provides you with a practical reference resource for your design toolkit.
Understanding SMT Footprints: The Foundation of Reliable Assembly
An SMT footprint represents the precise land pattern definition within your PCB design software that governs component placement and soldering characteristics. This critical design element encompasses several key components:
Pad Geometry:
The copper areas that establish electrical and mechanical connections between component terminals and the PCB substrate. Pad dimensions must account for manufacturing tolerances, component placement accuracy, and solder joint reliability requirements.
Component Outline:
The physical boundary that defines the component's occupied space on the board surface. This outline is essential for preventing mechanical interference and ensuring adequate clearance for adjacent components.
Pitch Specifications:
The center-to-center distance between adjacent pads, particularly critical for integrated circuits, where pitch variations can result in complete assembly failure.
Orientation Indicators:
Reference markers, such as pin-1 designators or polarization symbols that ensure correct component placement during assembly operations.
Even minor deviations in these parameters can trigger assembly defects, including tombstoning, insufficient solder joints, or electrical shorts, making footprint precision a non-negotiable aspect of professional PCB design.
The Manufacturing Impact of Footprint Accuracy
Incorrect footprint specifications extend far beyond simple soldering challenges, often compromising entire production cycles with significant cost implications:
Assembly Process Efficiency:
Inaccurate footprints frequently result in scrapped PCBs and unusable components, directly impacting machine utilization, increasing manual rework, and affecting project economics.
Schedule Adherence:
Assembly line disruptions caused by footprint errors can cascade through manufacturing schedules, affecting delivery commitments and customer satisfaction metrics.
Cost Escalation:
Engineering change orders (ECOs), rework operations, and potential redesign requirements can dramatically increase project costs beyond initial budgets.
At PCB Power India, our extensive manufacturing experience has demonstrated that proactive footprint verification during the design phase consistently prevents these downstream complications. We advocate for comprehensive footprint validation as a standard practice before initiating fabrication or SMT assembly processes.
Essential SMT Package Types: A Technical Reference
Understanding the dimensional characteristics and application contexts of commonly used SMT packages is crucial for design engineers:
Component | Dimensions (mm) | Notes |
1206 Resistor | 3.2 x 1.6 x 0.55 | Standard resistor; watch for orientation space |
SOIC-8 | 5.0 x 3.9 x 1.27 (pitch) | Common for op-amps, EEPROMs |
SOT-23 | 2.9 x 1.3 x 1.0 | Small signal transistors, low-power ICs |
QFN-64 | 8 x 8 x 0.8, 0.4mm pitch | High I/O count, thermal pad critical |
SMA Diode | ~5.0 x 2.8 x 2.4 | Be careful with the pad length for reflow |
MELF | ~5.0 x 2.5 | Cylindrical; needs a specific pad shape |
TQFP-48 | 7 x 7 x 1 , 0.5mm pitch | Microcontrollers and logic ICs |
This represents a subset of the comprehensive SMT package library. For detailed specifications covering 25+ package types with technical diagrams and optimized land patterns, refer to our complete SMT Footprint Guide available for download.
Critical Design Considerations
Professional PCB design requires attention to several technical aspects that can significantly impact assembly success:
Datasheet Verification:
Default library footprints may not reflect component-specific requirements or manufacturer recommendations. Always cross-reference component datasheets for accurate dimensional specifications.
Vertical Clearance Analysis:
Component height constraints become critical in high-density designs where vertical space is limited. Consider Z-axis clearance during component placement planning.
Thermal Management:
Heat-sensitive packages such as QFN and VSON often require thermal pads or vias for effective heat dissipation. Omitting these features can result in thermal performance degradation.
Fine-Pitch Accuracy:
Modern integrated circuits with sub-millimeter pitch requirements demand precise pad positioning. Small dimensional errors can prevent successful assembly.
Professional Design Methodologies
Implementing industry-standard design practices ensures reliable manufacturing outcomes:
IPC-7351 Compliance:
Adherence to IPC-7351 standards provides validated pad geometries and land pattern dimensions based on extensive industry testing and statistical analysis.
3D Modeling Integration:
Utilizing three-dimensional component models within your EDA environment enables comprehensive fit analysis and mechanical interference detection.
Design for Manufacturing (DFM) Analysis:
Systematic DFM evaluation identifies potential manufacturing challenges, including solder mask registration issues and silkscreen conflicts before fabrication.
Collaboration with Assembly Partners:
For advanced packages including BGA, QFN, and custom components, early consultation with your assembly provider can prevent costly design iterations.
Comprehensive Reference Resource
We have developed a technical reference guide containing detailed specifications for over 25 SMT package types, including:
- Precise dimensional data with manufacturing tolerances
- Optimized land pattern geometries per IPC standards
- Component-specific assembly considerations
- Visual diagrams with critical dimension callouts
This resource serves as a practical design reference for engineering teams working with surface-mount components across various application domains. Click here to download SMT Footprint Guide.
Conclusion
While SMT footprints may represent small elements within your overall PCB design, their influence on manufacturing success is substantial. Proper footprint design and verification practices form the foundation of reliable, cost-effective PCB assembly.
The investment in thorough footprint validation during the design phase consistently yields significant returns through reduced manufacturing risks, improved first-pass yield rates, and enhanced product reliability.
For technical consultation regarding footprint verification or manufacturing readiness assessment, our engineering team is available to support your design requirements.
PCB Power India - Excellence in PCB Manufacturing and Assembly
Technical Support: [email protected] | [email protected]
Technical Resources: www.pcbpower.com
Ready to advance your project? Request an instant quote today.
Frequently Asked Questions (FAQs)
Q1: What is the difference between SMT and THT footprints?
A: SMT footprints mount components directly on the PCB surface using solder paste, while THT footprints use drilled holes for component leads. SMT offers higher density and automated assembly compatibility.
Q2: How do I choose the correct SMT footprint for my component?
A: Always check the manufacturer's datasheet for recommended land patterns and follow IPC-7351 standards. Consider pad size, spacing, and thermal requirements. Consult your assembly partner when uncertain.
Q3: What causes SMT component placement failures during assembly?
A: Common causes include incorrect pad dimensions, wrong pitch specifications, missing thermal pads, component height conflicts, and orientation errors. Poor footprint design causes ~30% of assembly defects.
Q4: What is IPC-7351, and why is it important for SMT footprints?
A: IPC-7351 is the industry standard for land pattern design. It provides validated formulas for pad dimensions based on component tolerances and manufacturing capabilities, ensuring consistent, manufacturable designs.
Q5: How do I verify my SMT footprint before production?
A: Key steps include datasheet verification, 3D modeling for fit analysis, DFM evaluation, and consultation with your assembly partner. Many manufacturers offer footprint verification as part of their DFM services.