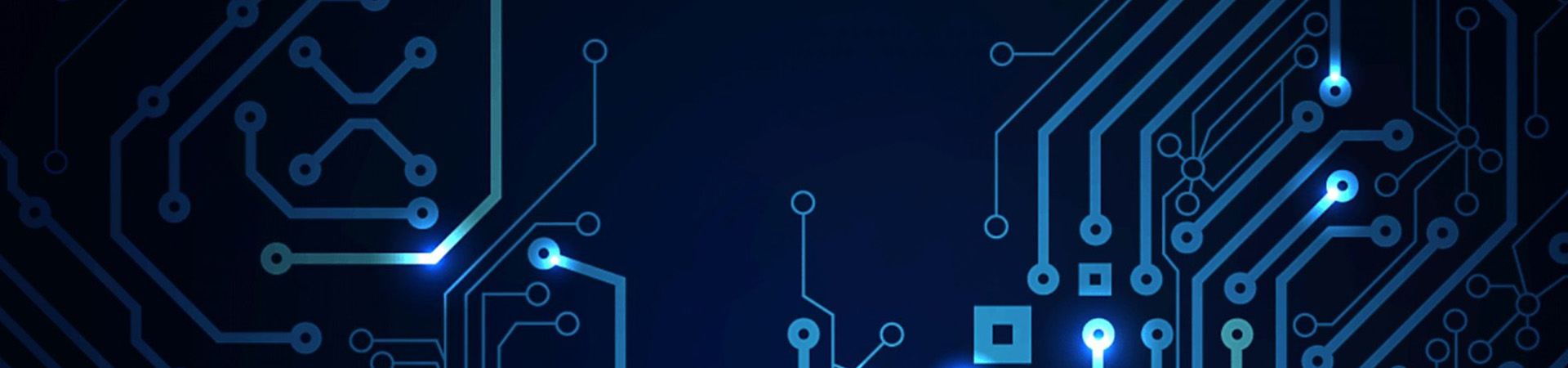
What is Warpage in PCB and Techniques to Avoid It
Imagine this: Even after flawless assembly, the board rocks on the table after reflow — a sign of trouble
Frustrating? Absolutely.
Costly? Without a doubt.
That slight bend, known as PCB warpage, often goes unnoticed until it starts affecting signal integrity, component alignment, and the overall efficiency of your production line. It's a subtle issue, but one that can derail both performance and timelines if left unaddressed.
Warpage is one of the most annoying and expensive problems to deal with in PCB manufacturing since it typically happens too late in the process to be fixed simply.
Why Does the Board Even Bend?
At its core, warpage is a battle of mismatched stresses. Fibreglass, copper, and resin all expand at different rates when things heat up. During soldering, the laminate is jolted from ambient to 240 °C in minutes, then yanked back down again. If one layer cools faster than its neighbors, it shrinks first and drags the whole stack in its direction. Cue the banana-shaped board that refuses to sit flat.
Techniques to Keep Boards Flat(ish)
Yes, physics can be cruel, but there’s a stack of practical fixes designers and process engineers can apply before the first panel hits the press.
1. Balance Your Layers Early
Symmetry is king. Match copper weights top to bottom and keep dielectric thickness uniform. Tempted to shove all the power planes on Layer 2 “because it’s convenient”? Resist. Future-you will thank present-you.
2. Use High-Tg Materials for Demanding Builds
A higher glass-transition temperature means less resin movement near reflow peaks. It’s pricier, sure, but so is discarding a batch of warped boards. Do the maths.
3. Pre-Bake Bare Boards to Drive Out Moisture
An eight-hour bake at 110 °C sounds dull, but it purges absorbed water and lowers the risk of steam-caused delamination. Skip it and watch the laminate bubble like pizza crust.
4. Panelize with Rigid Rails
Designers can add break-off rails along the lengthwise edges. These sacrificial strips stiffen the panel during reflow, keeping the product area flatter. Snapping them after assembly feels oddly satisfying, too.
5. Fine-Tune the Reflow Profile
A gentle pre-heat ramp (1–2 °C /sec) lets all layers reach equilibrium together. Likewise, a controlled cooldown reduces tension. Think of it as allowing the board to “stretch” before and after its high-temperature sprint.
6. Insist on Tight Press Controls in Fabrication
During PCB manufacturing in India, excessive lamination pressure can squeeze out resin and create voids that encourage warping. Clear press-cycle instructions, pressure, temperature rise, dwell, and keep vendors honest.
7. Post-Assembly Flattening
As a last resort, some assembly houses press mildly warped panels between heated plates for a “reset”. It’s not elegant, and repeated cycles degrade material properties, but it can rescue marginal product runs in a pinch.
Conclusion
Warped PCBs can delay timelines, increase costs, and complicate production unnecessarily. But here’s the good news: most cases of warpage are preventable. With the right choices in layer stack-up, moisture control, and thermal profiling, flat and reliable boards are within reach.
At PCB Power, we prioritize dimensional stability at every step — from fabrication to assembly — so you can focus on innovation, not rework.
Partner with us for your next project, and benefit from proven, warpage-resistant processes built right into our workflow. Visit our website to get an instant quote and keep your designs — and deadlines — on track.
FAQs
1. What is PCB warpage, and what causes it?
When a printed circuit board bends or twists because of uneven stresses during manufacturing or assembly, especially when it is heated and cooled, it is said to be warping.
2. How much bending is allowed for a PCB?
In general, a bow or twist of up to 0.75% of the board's diagonal length is acceptable. Anything more than that might make it impossible for assembly tools and parts to get to the right spot.
3. Does water make PCBs bend?
Yes, it can. Things like FR-4 soak in water over time. That moisture converts into vapour when it becomes too hot, which may cause the material to expand or fall apart.
4. What's the simplest approach to check for warping in a PCB at home or in a small lab?
Put the PCB on a flat surface, like a stone. Push down on one corner and see whether the other corner rises. If it moves like a seesaw, it's warped.
5. Are there any design guidelines that help keep warping to a minimum?
Yes, for sure. To keep items from warping, you should keep the copper distribution uniform, balance the layers, use high-Tg materials, and avoid uneven component clustering.
6. How does PCB Power keep things from bending?
We keep your boards flat and working by using exact manufacturing methods, controlling moisture, and keeping an eye on the temperature. This keeps warping to a minimum from the start.